Decommissioning of peat use in Finland
1.6.2021
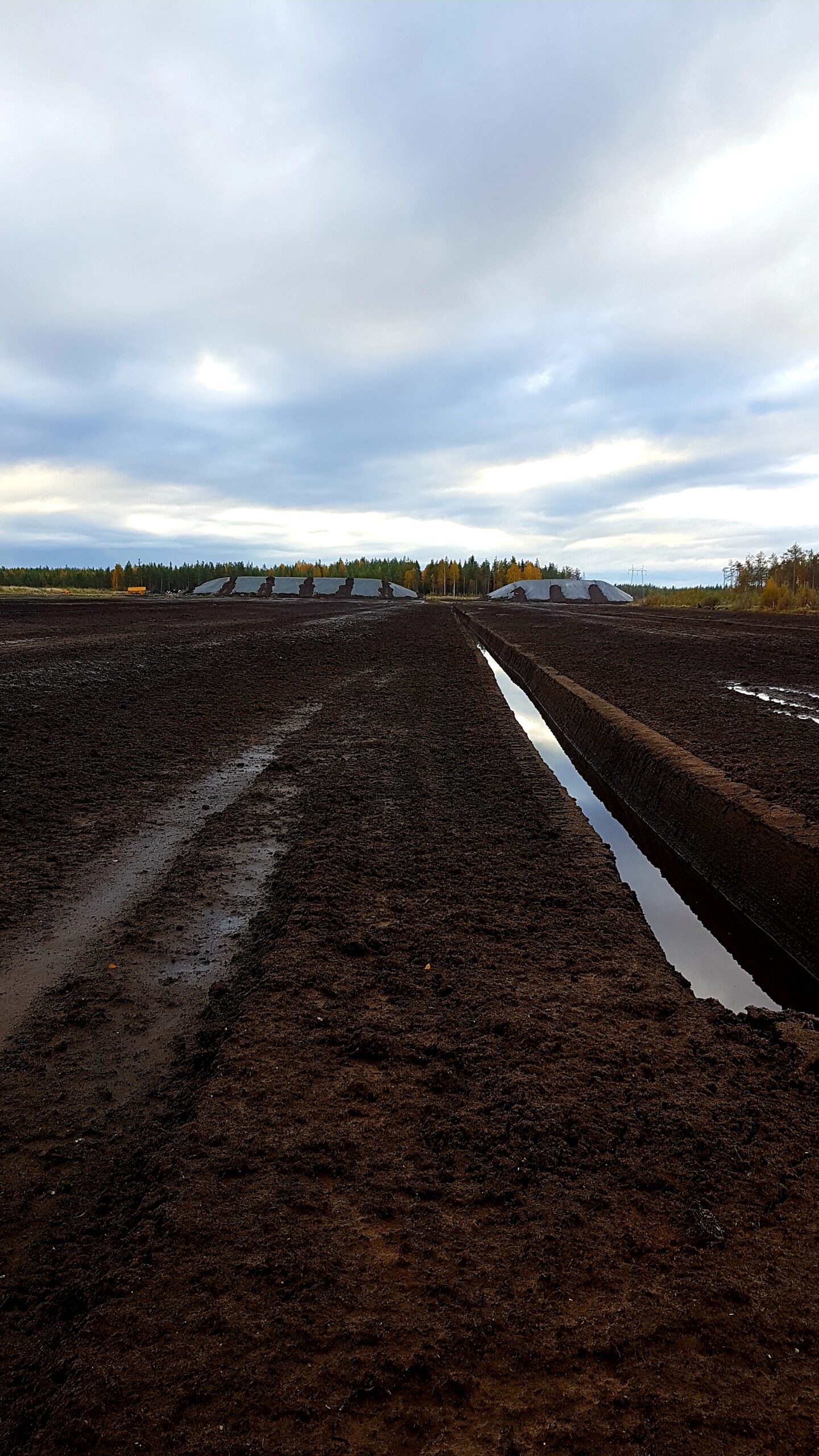
Decommissioning of peat burning – in a controlled way towards biomass
Finland intends to halve the energy use of peat by 2030. However, how the challenge is to be tackled over the next nine years is still open. In March, Minister of the Environment and Climate Krista Mikkonen stated that the government must make a clear plan for shutting down the energy use of peat. Where are we now? Last year, fossil fuels accounted for 13.8 per cent of Finland’s electricity production and 40 per cent of district heating was produced by burning peat, coal, oil and natural gas. Peat produces only about six percent of Finland’s total energy needs, but it accounts for up to one-fifth of the energy sector’s emissions – and 12 percent of Finland’s total emissions.
There are more than 50,000 hectares of peat production in Finland. About 90 percent of peat is burned for energy. It is five years since the Paris Climate Agreement was signed, but our government is still in the process of creating a plan for peat.
The keyword seems to be “controlled” downtime. Still, for example, the Confederation of Finnish Agricultural and Forestry Producers MTK described the downsizing of peat energy use as “reckless” in its December statement. The Finnish people also have an opinion on the matter: at the beginning of 2021, news was announced about the citizens’ initiative on ending the use of peat energy, which received the required 50,000 signatures and went to Parliament. According to the initiative’s proposal, peat should be phased out five years earlier than planned, ie by May 2025. Would it even be in a hurry? We believe that decommissioning peat use should be controlled and planned.
What happens when a power plant switches from peat to biomass?
In the 1970s and 1980s, peat-fired power plants were built in Tampere, Kuopio and Oulu, among others. Already in the 90s, boilers began to be converted into multi-fuel boilers, ie in addition to peat, power plants were ready to burn wood-based fuels. The forthcoming decommissioning of peat production will force power plants to look for new energy sources – and that means millions of investments in many locations. In practice, this might mean that, boiler technology, fuel reception system, conveyors and sampling system will be renewed in power plants. At the same time, environmental permits must also be updated, as the permit is always based on the fuel fractions and quantities burned.
As the material to be burned changes from peat to biomass, quality determination plays a significant role. The biomass to be burned enters the power plant in trucks, where one may contain forest residue chips imported from the vicinity, the other wood chips imported from Russia and the third, for example, forest industry by-products such as sawdust and bark. These loads can be very different in terms of moisture and energy content – the variation in individual loads can also be really large.
If we place two identical full trailer trucks carrying 150 cubic meters of fuel side by side, we will be able to concretize the difference: there are only about 1 to 3 percentage points difference in the moisture content of the peat truck load between the measurement points – at most only 5%. The moisture content of biomass, on the other hand, can vary between 30 and 60%. That is, the biomass load may be wet at one point of the truck running off the water and the sample taken from the other point may be relatively dry.
Peat is thus homogeneous as a fuel for power plants. When biomass is burned in a boiler instead of peat, the fuel is heterogeneous, the quality of which should be measured particularly carefully to determine the correct price for the load. Errors in sampling and moisture measurement accumulate as an additional cost to the power plant.
Winter has a major impact on biomass quality measurement
On the scale of power plants, small human errors can cause large differences in the material flows of thousands of tons. In Finland, one human thing to consider is winter: snow and ice inevitably affect winter moisture measurements. The largest errors occur in the actual sampling, but measurement errors are also caused by sample handling and storage.
It is not uncommon for tens of kilos of ice to fall to the unloading site when unloading a truck load. It is far from homogenous material. The example in the photo below shows the winter reality: the load is layered with ice, snow, wood chips and forest debris. If the load were manually sampled with a small shovel into the bucket right from the top of the cart – would the surface sample represent the moisture of the entire load?
Positive results from the change in Kuopio Energy
Kuopion Energia introduced an automated Q-Robot sampling robot in 2017 at its power plant. Production director Peter Seppälä states that the world was lying in a different position at the time.
– Compared to the plans of that time, the shutdown of peat burning will take place much faster under the guidance of emissions trading. At that time, Kuopion Energia was Prometec’s pilot project to solve the challenges of manual biomass sampling. Quite positive results began to show almost immediately, Seppälä says.
Kuopion Energia’s electricity and heat production is centralized at the Haapaniemi power plant and the Pitkälahti power plant. A total of about 14,000 truckloads of wood and peat arrive in Haapaniemi every year, producing 1.3 million megawatt hours of energy. This can be proportioned, for example, by comparing the need for an ordinary detached house: the annual energy demand for heating and hot water is about 20 megawatt hours.
– Manual metering and fuel moisture fluctuations produced us 50 gigawatt hours less energy per year than the price paid for the fuel. Roughly speaking, our annual fuel costs are in the order of EUR 25 million, and the percentage error is EUR 250 000. With Q-Robot, our savings over the past few years are worth millions.
– Significantly more fuel is needed during the winter. If we look at, for example, three months from June to August, during these three months the same amount of fuel is used to produce electricity and district heating as in two weeks in the winter, Seppälä concretizes.
A hall was built for Q-Robot in the area of the Haapaniemi power plant, where a truck arriving with biofuel will drive for weighing and automated sampling. The robotic auger takes several samples at randomly selected points and depths, and combines them into a representative sample of the entire load, following solid biofuel sampling and sample handling standards ISO 18135 and ISO 14780.
– In the past, sampling involved human errors and I also understand the power of fuel producers from a great point of view, because, for example, a few percent change in dry matter percentage has an effect of hundreds of euros on the price of fuel load, states Seppälä.
Q-Robot – what’s the question?
- The automated Q-Robot sampling robot takes a reliable and representative sample of the raw material load quickly before unloading it.
- Sampling works seamlessly with a variety of solid and crushed materials.
- In addition to the sampling unit, the Q-Robot includes a machine vision system that measures the volume of the load in real time
- Q-Robot can generate calculated load moisture data and energy content data immediately after sampling
- Samples taken by the Q-Robot can be analyzed immediately on site with rapid measurement equipment or taken to the laboratory for analysis.
Read more about Prometec’s solutions
- For power plants
- For pulp mills
- For mining industry
- For agroindustry
Henna Karlsson, CTO